What If Solving Climate Change Didn’t Require Sacrifice... But Robots? - Part 1: Construction.
From 3D Printing Green Cities to Humanoid Robots for Construction: Where are the billionaire investing next?
We’ve been told climate change means sacrifice — less meat, less travel, less comfort.
What if the real solution isn’t sacrifice... but smarter machines?
Construction is being disrupted. Quietly, profoundly, and globally.
Construction is a $10T opportunity ripe for climate + AI + robotics convergence.
Southeast Asia is urbanizing faster than any other region.
Scarcity of skilled labor, rising materials cost, climate shocks — perfect storm = automation moment.
"In 5 years, we went from selling 3D printers for the home—to 3D printing homes."
— Philip Lund-Nielsen, Co-Founder of COBOD
When I visited a robot-built house in California, it felt like stepping into 2042.
Earlier this year, a former NASA engineer created the world first wildfire-proof home in Los Angeles. In the meantime, Siam Cement Group (SCG) and COBOD created the world’s first 3D printed two-story medical center in Thailand. Meanwhile, in Europe, Leko Labs is using carbon-negative wood-based systems to replace concrete and steel. And on the ground in California, Truebeck Construction is deploying cutting-edge robotics and prefab systems to deliver some of the most complex, sustainable buildings in the United States.
For the past year, I sat down consecutively with the leaders behind these innovations:
Sean Truesdale, CEO at Truebeck, San Francisco, USA.
Max Gerbut, CEO at Haus, Los Angeles, USA.
Timothy McCaffery, Director of Investment at SCG, Thailand.
Philip Lund-Nielsen, Co-Founder of COBOD, Miami, USA.
So, what is really happening behind the scenes in this very opaque construction industry—and how the convergence of automation, materials science, and visionary builders is changing how the world gets built, making a few lucky investors billions.
And in this essay, we’ll dive into this rabbit hole.
The Billionaire Blueprint: Where The Capital Is Heading Next
For decades, climate action has been framed as a tradeoff.
Use less. Fly less. Build less. Sacrifice more.
But what if the answer wasn’t austerity… but automation?
From Elon Musk’s Tesla Bot to Jeff Bezos' bets on prefab housing, billionaires are increasingly shifting climate capital toward robotics—especially in construction, one of the most labor intensive and carbon-intensive industries on Earth.
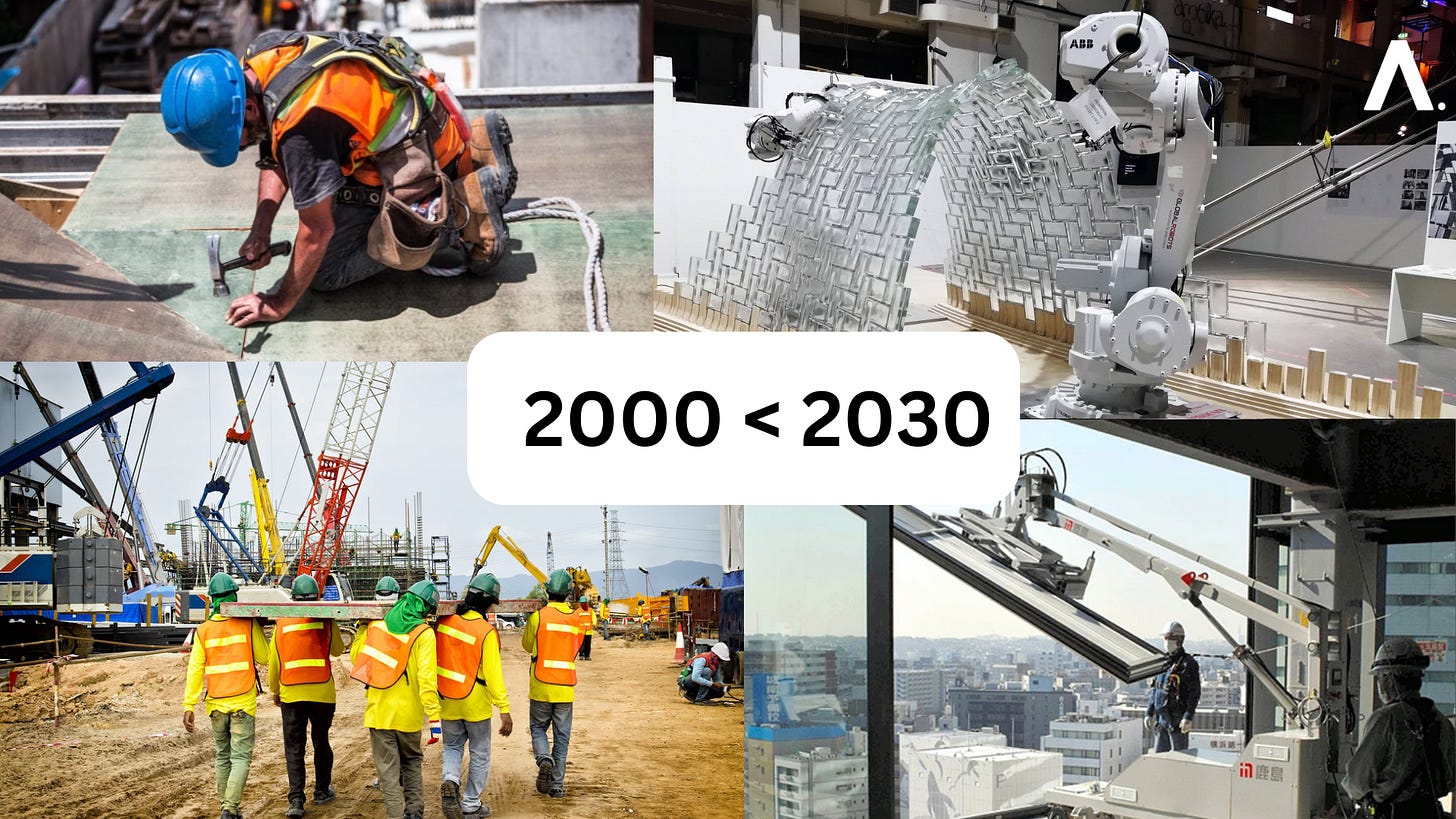
Why? Because the world is in a race to build billions of square meters of new housing, infrastructure, and climate change resilient spaces… and we don’t have the labor, materials, or time to do it the old way.
Southeast Asia urbanizing at the rate of one NYC per year, the opportunity to build smarter, greener cities has never been more urgent — or more lucrative. Source
We need to build:
Faster
Smarter
Cleaner
And future-proofed for fire, flood, hurricanes, and energy volatility
That’s exactly why billionaires, family offices, and institutional investors are:
Funding robotic 3D cement printers like COBOD
Backing fireproof & self-sufficient housing startups like Haus.me
Partnering with smart builders like Truebeck Construction
Exploring climate-resilient real estate as a defensive asset class
This is not a niche. This is a new category.
Why Construction Needs Disruption—Now
The global construction industry is worth over $12 trillion annually and underpins almost every human system. Yet it remains one of the least digitized, least automated, and most carbon-intensive sectors on the planet.
“People are still building homes with their bare hands,” said Philip Lund-Nielsen of COBOD. “It’s insane how manual and inefficient this still is.”
Meanwhile, buildings and construction account for 40% of global emissions. As cities expand, climate refugees migrate, and infrastructure ages, the demand for rapid, sustainable construction is only accelerating.
The old methods won’t scale. The new ones?
They're already here—and billionaires are paying attention.
Case Study #1: SCG and COBOD Print a Medical Center in Thailand
In Saraburi, Thailand, Siam Cement Group (SCG) and COBOD built the world’s first 3D printed two-story medical center—a 345m² facility constructed using COBOD’s BOD2 printer and SCG’s proprietary 3D printing mortar.
“It’s not just a prototype—it’s a real, seismic-resistant structure built faster and with less waste,” said Philip.
The medical center features curved, organic walls, which would be cost-prohibitive using traditional formwork. Instead, with robotic layering, it becomes both a design advantage and a functional upgrade.
“We aim to make 3D printing the new standard across ASEAN,” added SCG’s Director of Fabric Concrete Technology, Chalermwut Snguanyat.
Case Study #2: Haus.me and the Rise of Wildfire Proof Smart Homes in Los Angeles
Or maybe, in some cases, we won’t even need a construction site? What if we could manufacture a house and then ship it?
If COBOD represents large-scale robotic construction, Haus.me tackles the opposite frontier: off-grid, extreme weather resilient, energy autonomous living.
Founded by Max Gerbut, Haus.me builds solar-powered, extreme-weather-proof homes that are:
Resistant to wild fires & Category 5 hurricanes
Fully off-grid
Printed and fabricated in a factory
Shipped worldwide ready-to-live
Controlled by an onboard AI for temerature, energy, and air quality
“We’re building freedom,” Max says. “Freedom from the grid, from carbon, from climate risk.”
These high-tech homes appeal not only to preppers and digital nomads—but also to climate-conscious family offices, crypto millionaires, and real estate developpers hedging against instability in energy, supply chains and the global geopolitics.
Imagine:
Your backup residence is solar-powered
Your home is your battery
Your house is smarter than your car
This is no longer sci-fi. It’s being delivered today.
Case Study #3: Truebeck Construction Brings It to Scale
Tech is great—but someone has to sell it, integrate it and build it at scale. That’s where Truebeck Construction comes in.
Known for its work as contractor to build offices for Apple (yes the Cupertino one!), Google, and Open AI, Truebeck is integrating:
Modular systems
Robotic layout tools
Digital twins
On-site automation
They work with forward-thinking firms and help deploy tech like COBOD printers or Haus.me modules within the constraints of building codes, timelines, and budgets.
“We’re the connective tissue between frontier tech and real-world implementation,” says one Truebeck partner, who will speak at our upcoming San Francisco Family Office Summit.
They are proving—right now—that climate-resilient construction isn’t a pitch deck fantasy. It’s a jobsite reality.
2035: The Robotic Jobsite Becomes Normal
When I asked Philip what a job site would look like in 2035, he painted a powerful vision:
“Imagine a swarm of machines—one robot prints walls, another installs insulation, another paints, another lifts roof panels. All coordinated digitally. That’s where we’re headed.”
It’s not far off.
Fast forward 10 years.
You roll up to a construction site—no dust, no dozens of workers, no scaffolding.
Instead, you see:
A COBOD printer building multi-story frames
A Civ Robotics rover marking utility trenches
A Haus.me home arriving on a flatbed
A Zauben’s drone installing rooftop solar on a green roof
And Truebeck logos everywhere, operating the entire construction site.
This is not hypothetical. It’s already happening in pilots around the world.
The only question is: Will you sit & watch or invest now and profit from it?
My Take as an Investor
As someone who has written a book on The Adaptive Economy, invested in climate tech, and built coalitions across Asia and North America—this trend feels inevitable.
Now if you were a Seed investor of COBOD, this is the return on investment you would have got right now:
Forget about ETFs: Current ROI is already 50x–75x for early Seed investors.
If COBOD exit at $5B with an IPO: Which is current trajectory, Up to 165x ROI.
Alongside 2 billionaires & 7 family offices, in October 2022, Holcim, one of largest strategic player in the industry invested in COBOD.
COBOD is one of those frontier hardware startups where Seed round investors could see moonshot returns.
COBOD shows what’s possible when robotics meet green real estate.
Haus demonstrates that sustainability can scale with green modular housing.
Truebeck proves that innovation works in practice on large real estate projects.
Together, these firms point to a decarbonized, automated, and climate-resilient future of construction.
The Construction Tech Stack: Build Faster. Smarter. Greener.
Together, COBOD, Haus.me, and Truebeck represent a new construction stack:
COBOD = Robots & large-scale printed infrastructure
Haus.me = AI-powered, autonomous, off-grid living
Truebeck = Smart execution, scalable delivery
This stack is not just a solution to housing demand.
It’s a new asset class for investors.
It enables:
Disaster-resilient cities
Net-zero suburbs
Mobile climate migration hubs
Energy-independent housing portfolios
“I want to see COBOD printers on every major construction site,” Philip told me. “Like cranes or excavators.”
Final Thoughts: This Is How We Win
For too long, climate solutions have been framed as limits.
Less flying. Less heating. Less growth.
But what if the real answer is more?
More intelligence. More efficiency. More autonomy. More imagination.
This is how we build homes in wildfire zones.
This is how we scale green cities across Southeast Asia.
This is how we give billions access to safety, shelter, and sovereignty.
And it starts with this question:
What if solving climate change didn’t require sacrifice… but robots?
This time, billionaires are getting in early. Why not us?
Let’s build.
Meet the Builders of the Future, this April.
We’ll be featuring Truebeck, SCG, Haus and Zauben at the upcoming Family Office & Investors Summit during Climate Week in San Francisco this April 22nd.
If you’d like to meet their teams, see live demos, or explore investment and commercial partnership opportunities—get your tickets.
Fight the good fight.
— Djoann Fal